Aluminum Extrusions
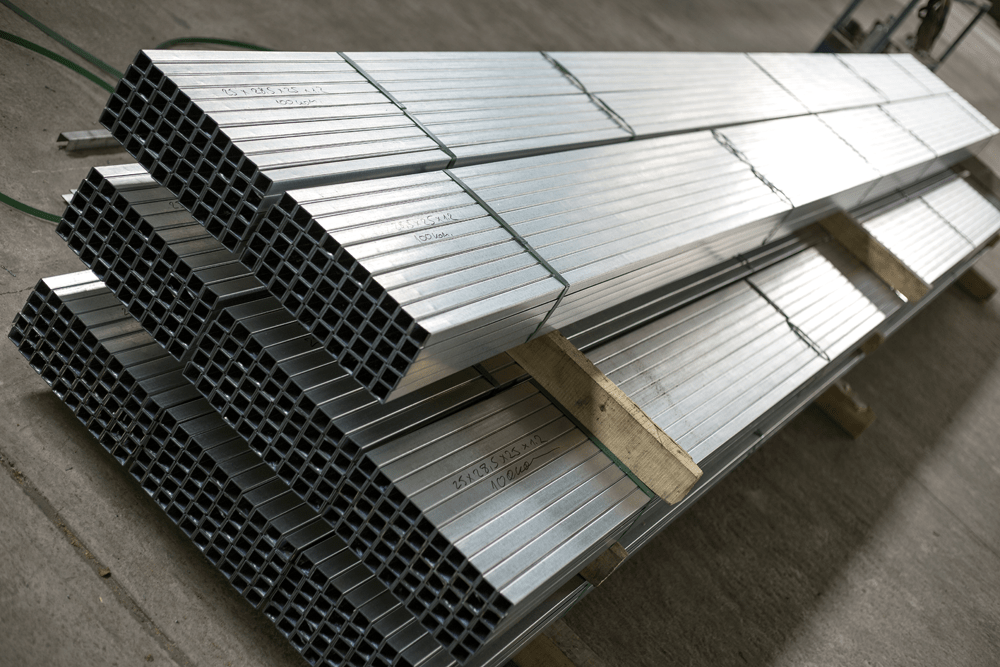
Aluminum Extrusions
Aluminum extrusion is a method used to transform aluminum alloy into various objects that have a definitive cross-sectional profile for numerous uses. The process of aluminum extrusion consists of the following: After the shape of the die has been designed & created, a cylindrical billet of aluminum is heated. Once the billet is heated to 800 deg. F – 925 deg. F it is then moved to a loader. At this time a lubricant is applied to the aluminum billet which will prevent it from sticking to the ram; handle, or the die itself. Pressure is then added to a dummy block via a ram, which forces the aluminum billet through the die. Nitrogen is then introduced to prevent the formation of oxides, creating an inert atmosphere and increasing die life. Once the extruded part passes through the die opening it is then put on a cooling table which has fans to cool the aluminum extrusion. Once cooled, the aluminum extrusion is moved to a stretcher for straightening and hardening. The extrusion is now ready for the age ovens where it is heated, hardening the aluminum by speeding the aging process.