Nitrogen Generators and Holiday Electronics (Surface Mount Technology)
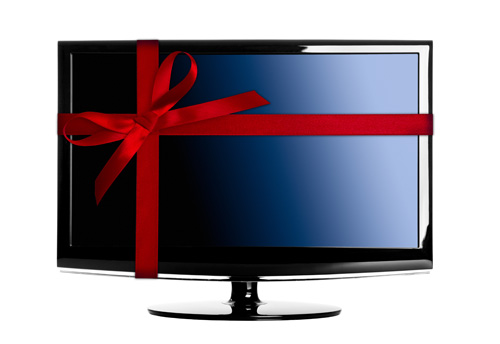
The love affair with tech gadget Holiday gifts continues. Even as total retail holiday spending is projected to decline, the first big sales weekend – from “Grey” Thursday to “Cyber” Monday – is booting up to a 2.5% increase in purchases of consumer electronics over last year, says the Consumer Electronics Association.
Retailers are fueling the surge with great deals on high profile items. One deal, copied by more than one store, presented a name brand 50” screen TV to vigilant shoppers for just over $200. A similar set would have sold for 5 or 10 times that price just a couple years ago.
While it’s not uncommon for retailers to lure bleary eyed bargain hunters with such loss leaders, it’s a reduction in manufacturing costs that help make these big screen dreams a reality. For example, many electronics manufacturers the introduction of nitrogen to the SMT, or Surface Mount Technology, process has reduced costs and improved efficiency.
In a typical SMT process a bit of solder paste is applied before a component is placed on the board. The board is sent through a reflow oven, which includes an initial heating zone to bring the temperatures up slowly and a zone where temperatures are high enough to melt the paste. Since solder pastes are metal based, when they are exposed to heat and oxygen there is an opportunity for corrosion. The corroded solder paste is called dross and is responsible for a great deal of waste in an SMT process.
Corrosion can cause the need for some connections to be reworked after the reflow oven and the wasted solder paste needs to be cleaned from the board – adding labor cost to each piece. As solder paste is not inexpensive, wasting it also adds cost.
This is where nitrogen comes in. When the atmosphere in a reflow oven is flushed with N2, the oxygen is displaced and solder paste corrosion is greatly reduced. The cost of nitrogen is out paced by the savings that come from reduced solder waste and poor connections.
The cost benefit of introducing nitrogen to a reflow oven becomes even more dramatic for facilities that produce their own supply of N2 gas. A nitrogen generator, basically a filter that separates nitrogen from compressed air, can produce a clean supply of gas at 1/3 or less than that of delivered supplies.
Like any capital investment it’s important to not over or under buy for your application. The good news is that there are companies, such as Compressed Gas Technologies, with an understanding of both how reflow ovens work and what specifications are needed to supply them with nitrogen.
Saving 70% or more compared to the price of delivered nitrogen is a door buster every plant manager can appreciate.