Autoclaves and the Tour de France
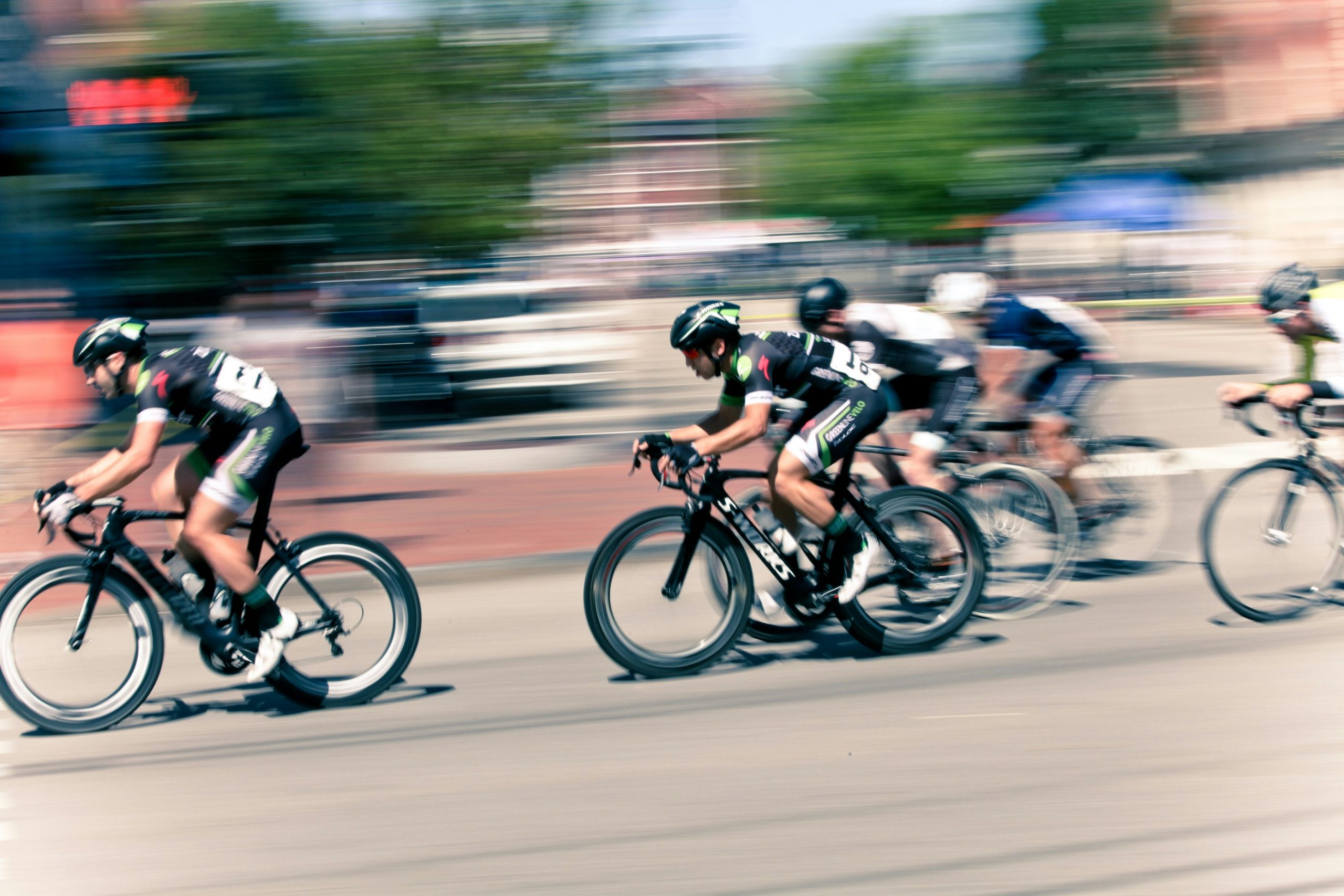
Back in 1902 a young cycling journalist, Geo Lefvere, suggested a multi-stage race throughout France as a method to increase flagging sales of the upstart sports paper L’Auto. In 1903 Maurice Garin won that first Tour de France, averaging just under 20 mph during the final stage, on a steel frame bike sporting wood rimmed wheels.
Those early days were rough on competitors of The Tour. Garin was stripped of his 1904 win for cheating and he wasn’t the only one. As some stages were raced at night, away from the prying eyes of race officials, fans hoping to give their rider an edge would block roads and beat up opposing cyclists.
Just as the sophistication of cheating has progressed, with very few actual rider assaults expected during this year’s race, so has the construction of the modern racing cycle. Aluminum usurped steel in frame construction which has since been replaced by carbon fiber.
Along with advances in wheel and mechanical design, these ultra-light frame constructions have steadily emaciated the two wheeled steeds ridden in this most prestigious of races. From the relative hefty 24 pound bike that won The Tour in 1965 to the svelte 14.5 pound cycle used in Lance Armstrong’s now-invalid Tour win in 2004 (restrictions have since set the minimum weight at 15 pounds), manufacturers have benefited from the amazing properties of carbon fiber technology.
The high strength, low weight, and malleable building material isn’t restricted to biking alone. The aerospace industry, for example, makes use of carbon fiber in construction of all sorts of aircraft, from fighter planes to commercial jetliners. But working with this wonder material isn’t without its dangers.
A common step in the production process of carbon fibers components is a high pressure, high heat cure in an autoclave. In the aerospace industry, autoclave vessels can be huge (the largest to date is 30 feet in diameter and resides at the Boeing facility in Charleston, SC).
The off-gas of some materials treated at high heat can be flammable. And since this operation is done at higher pressures, 300 psi or more, the potential for combustion when air is used as the pressurizing agent is high. Many users of large autoclaves have turned to nitrogen as a pressurizing agent, reducing the overall oxygen in the autoclave and the potential for a disastrous fire.
When you think about a chamber big enough to hold body parts of a commercial jetliner, you get an impression of the amount of nitrogen needed to pressurize the internal space of a large autoclave. That amount of nitrogen can be difficult and very costly to procure. For manufacturers who turn the autoclave often, requiring frequent pressurization, a nitrogen generator can become an integral component in the process.
The typical nitrogen delivery system will include a first stage, low pressure air compressor followed by a nitrogen separation system (nitrogen generator), then a high pressure booster and, finally, a storage tank sized to hold enough gas to do the job.
The on/off nature of this type of nitrogen use creates opportunities for inefficiencies in the system. It takes an experienced team to properly size and design a system capable of keeping up without impractical waste. Compressed Gas Technologies has been doing that exact work for over a dozen years and are experts in both membrane and pressure swing adsorption (PSA) style nitrogen generators.
There’s no doubt that today’s elite cyclists are among the toughest people on earth. But their predecessors from a century ago were not exactly soft either. Monsieur Garin was a smoker, rode a bike weighing more than 30 pounds, and during a 24 hour endurance race – which he won by being only one of two riders to finish – listed “lots of strong red wine” among his consumables. Perhaps we’ve been going about this sports drink craze all wrong.